Industry News
Development of EAF Steelmaking
Author : Hani Time : 2021/02/22
The development of EAF steelmaking can be divided into three stages
(1) Research stage (from 1800 to 1900)
In 1800, the Englishman Humphrey Davy invented the carbon electrode; in 1849, the Frenchman deprez used the electrode to melt metal; in 1866, the German Werner von Siemens invented the electric energy generator; in 1879, the German C Williams invented the carbon electrode In 1885, ASEA (General Electric) Company of Sweden designed a DC electric arc furnace, and in 1888, Paul H In 1889-1891, synchronous generators and transformers were widely used; in 1899, helault successfully developed AC arc furnace; in 1900, helault began to use AC arc furnace to smelt ferroalloy; in 1899, helault began to use AC arc furnace to smelt ferroalloy;
(2) Primary stage (from 1900 to 1960)
In 1905, German R. lindenberg built the first two intersecting current electric arc furnace (hailault type) for steelmaking. The furnace features square electrode, manual lifting of electrode, fixed and immovable furnace cover, and manual feeding from the furnace door. In 1906, lindenberg successfully refined the first furnace of molten steel and poured it into ingot, thus ushering in a new era of EAF steelmaking From 1909 to 1910, Germany and the United States made 6 T and 5 t three-phase AC arc furnaces respectively and put them into operation; in 1920, automatic electrode lifting regulator was adopted to improve the speed of electrode lifting; in 1926, German Demark changed the furnace cover to moving out type and realized top charging for the first time; in 1930, the furnace body opening type electric arc furnace appeared; in 1936, German made 18 t furnace cover rotating type electric arc furnace Electric arc furnace; in 1939, the Swede trevors put forward the idea of electric arc furnace electromagnetic stirring; in 1960, in order to balance the three-phase reactance, the United States appeared short net equilateral triangle arrangement; at this stage, due to the limitations of power, electrode, oxygen consumption level, furnace capacity, etc., the cost of steelmaking is much higher than that of open hearth furnace, so it is only suitable for smelting alloy steel and special steel. With the outbreak of the Second World War, the output of EAF steel increased rapidly.
(3) Great development stage (from 1960 to now)
As the internal structure of iron and steel industry changed greatly in the mid-1950s, and LD converter replaced the leading position of Oh open hearth furnace in steelmaking, LD furnace can not use scrap as raw material as open hearth furnace, so with the gradual withdrawal of open hearth furnace from steelmaking stage, the problem of surplus scrap becomes increasingly prominent. Therefore, EAF furnace is required to play a role in smelting alloy steel at the same time It is the task of smelting ordinary steel. In this way, the development direction of how to greatly improve productivity and reduce production costs is proposed for EAF. In 1964, W.E. Schwabe of American carbide company and C.G. Robinson of Northwest steel wire rod company jointly put forward the concept of ultra-high power of electric arc furnace, and carried out experiments on two 135t electric arc furnaces with different power levels. Soon UHP operation was popularized in countries all over the world, which greatly shortened the smelting time from 3-4 hours to 2 hours (power level) 500kVA/t)。 Since 70s, in order to maximize the efficiency of the transformer, a series of related technologies have been developed around the aspects of how to further improve the power utilization ratio and the time utilization rate. For example, the furnace wall, the furnace cover water cooling, the long arc foam slag operation, the oxygen burning nozzle, the eccentric furnace bottom tapping, the scrap steel preheating, the bottom blowing, the double shell electric arc furnace and so on. Therefore, the power level of the transformer reaches 800-1100kva / T, the smelting time is further reduced to less than 1 hour, and the power consumption is reduced to less than 400kwh / T. The process mode of "scrap preheating electric arc furnace external refining continuous casting hot delivery rolling or continuous rolling" has been gradually promoted in special steel plants, and the electric arc furnace has evolved into a simple scrap rapid melting equipment. In order to fundamentally overcome the hot spot problem of furnace wall caused by arc instability and three-phase power imbalance of AC ultra-high power EAF and the severe impact (flicker problem) on the former power grid, the research on DC EAF was started in the 1970s and put into industrial production in the mid-1980s. Since then, the EAF has developed in both AC and DC.
To sum up, in more than 100 years since the birth of EAF steelmaking, from the beginning of small EAF specialized in smelting alloy steel, to the later change to large EAF for smelting alloy steel and plain carbon steel, until the recent ultra-high power large (AC, DC) EAF only used as scrap melting equipment.
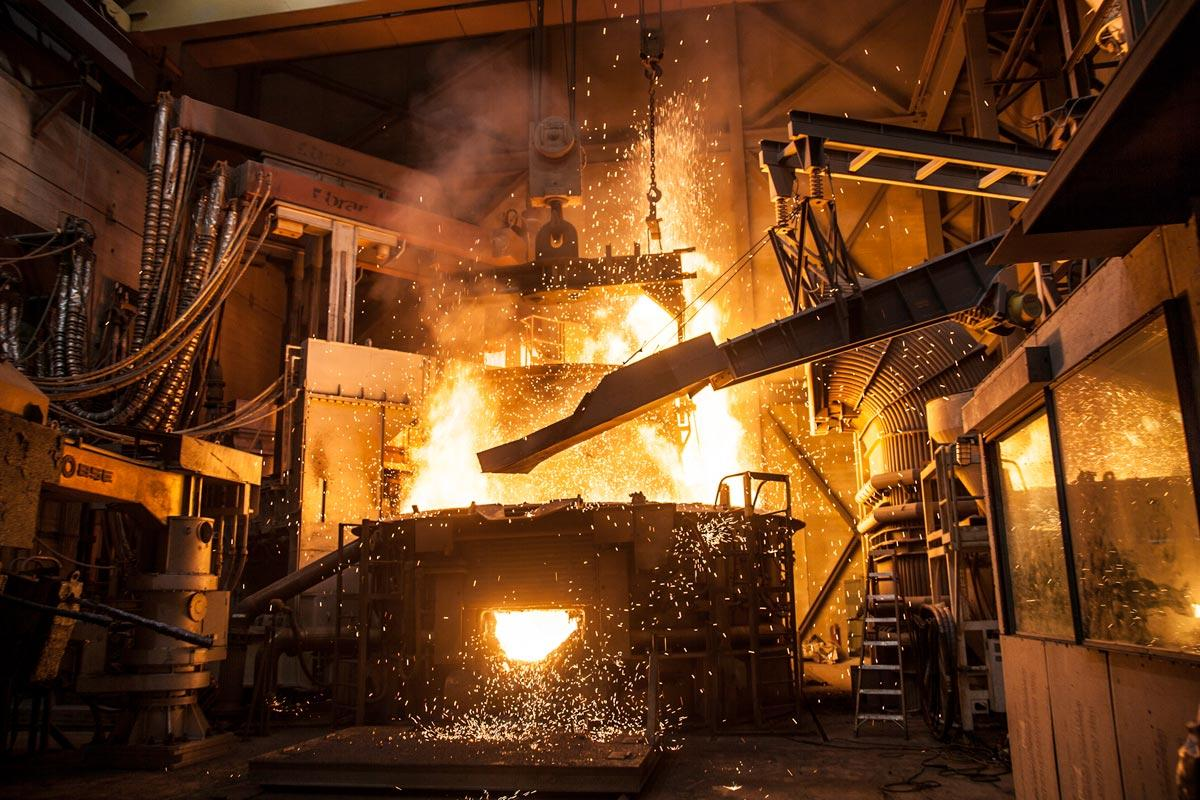
TAG:  EAF steelmaking electric arc furnaces (AC, DC) EAF small EAF large EAF preheating electric arc furnace